INORCOAT: How to Make Minting More Sustainable
by Ursula Kampmann
Are you annoyed by all the laws that make our lives more difficult but have no positive effect? Here’s an example of a law that actually makes sense: the planned ban on chromium (VI) electroplating is helping an innovative technology to make a breakthrough – and this development brings decisive advantages for the minting industry. Romain Waidelich of INORCOAT takes us behind the scenes.
Content
Chromium (VI) has been deemed an environmental pollutant by the EU since 2017. And there are good reasons for this. The substance is considered toxic and carcinogenic. Its inhalation, in particular, leads to an increased risk of lung cancer. For this reason, from 21 September 2024, chromium (VI) can only be used in Germany if you have a special authorisation. To apply for this, extensive documentation – we are talking about several hundred pages of documents – must be submitted to the ECHA, the European Chemicals Agency. And even if a company meets all the requirements for an exemption, there is no saying whether it will obtain the authorisation in time as the ECHA is currently flooded with applications, all of which need to be thoroughly assessed…
Why Is Chromium (VI) Needed for Coin Production?
German mints will also be affected by the proposed ban. After all, chromium electroplating, which produces chromium (VI) as a by-product, is a key process in the manufacture of minting dies. The dies are coated with a layer of chromium before being used in a minting press to make them more durable. This chromium (VI) coating prevents what numismatic auction houses refer to as a “tired die”. It ensures that the minting die does not wear out as quickly and that more coins can be struck from a pair of dies before they need to be replaced.
Applying chromium to a die requires – simply put – a long series of alternating baths of acid, lye and rinsing liquids. A pair of dies passes through all these baths to be coated with chromium by electrolysis. Of course, excellent water treatment methods exist by now. But as Günther Waadt, the former head of the Bavarian State Mint, explains: “Electroplating is always a bit messy, no matter how meticulously you are about cleansing. Acids are going to splash around somewhere.”
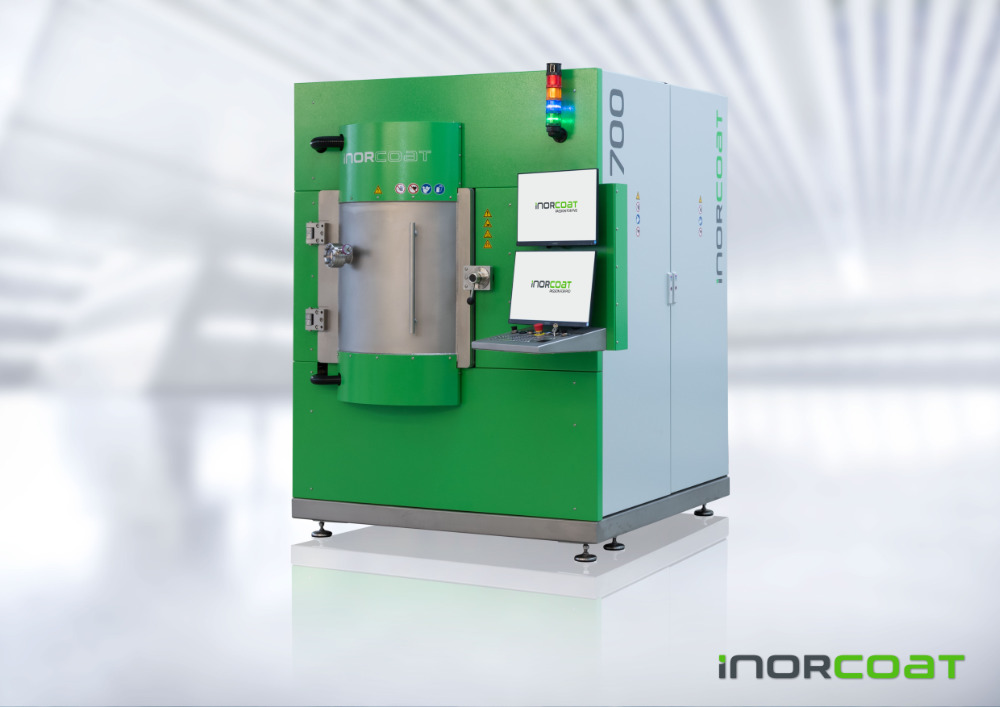
Coin dies get their PVD coating in machines like this one: the compact MS 700 by INORCOAT. Photo: INORCOAT.
PVD Coating as an Alternative to Electroplating
In recent years, PVD coating has established itself as an excellent alternative to electroplating. PVD is short for physical vapour deposition. This means that metal vapour is produced in a machine and deposited on the object as a thin, strongly adherent layer. Any metal can be applied to the object – either in its pure form or as an alloy. The process is carried out in a high vacuum chamber and is, of course, much more complicated than this brief explanation would suggest. After all, every coating requires its own formulation. This determines the composition of the materials and the order in which they are applied.
Romain Waidelich explains that the quality of a coating depends largely on the cooperation between the customer and the developer. “At INORCOAT, we create a coating that exactly meets our customer’s needs. To do this, we carry out carefully controlled test series with material samples and prototypes from our customers. This allows us to determine the perfect PVD configuration for each application.”
In practice, this means that the best results are achieved when the PVD system is perfectly tailored to the customer. “If a single gas point is needed in a small system, only one valve terminal will be installed. This reduces complexity and costs,” explains Romain Waidelich. “If the customer wants to add the possibility for other treatments at a later time, we can extend all our standard systems to meet these new requirements. This gives customers maximum flexibility.”
A New Record: 14 Million Croatian Euro Coins Struck with One Pair of Dies!
The records set by the Croatian Mint when introducing the Euro show what a perfect configuration can achieve. And such a record was necessary! The choice of the design was complicated, sparked public debate at home and abroad, and as a result the production of the coin dies was postponed again and again. It was not until 18 July 2022 that the minting of 420 million Croatian euro coins could officially begin. A large part of the coins had to be in banks and supermarkets by 1 January 2023. Meeting this deadline was a logistical challenge for the comparatively small Croatian Mint – but it was one they mastered brilliantly.
After all, Croatian minting engineers are among the best in the world. They proudly present one technical masterpiece after another. Be it “Contour Necktie” of 2023 – two special shape coins that can be put together to form a new object – or the world’s smallest coin: Croatia is using innovative technology to shape the coins of the future.
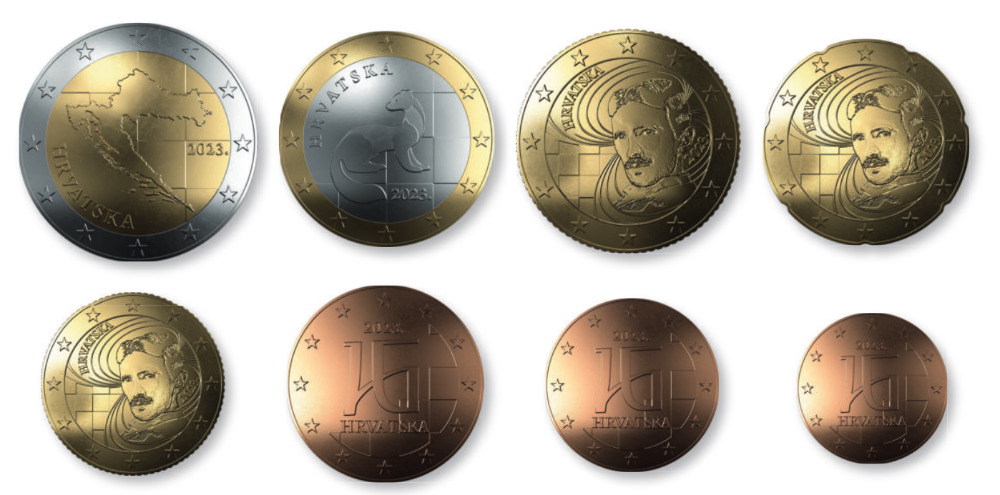
The Croatian euro coins were minted with dies that were particularly durable thanks to an INORCOAT PVD coating. Photos: Croatian National Bank.
That is why Romain Waidelich’s concept met with a receptive audience. The decision for the new system was made shortly before the introduction of the Euro, and it did not disappoint. The number of coins struck from a single pair of dies increased dramatically thanks to INORCOAT. Typically, minting dies for circulation coins are replaced after 200,000 to 300,000 strikes. Thanks to the new coating, this was not necessary. Romain Waidelich was delighted: “PVD coating made it possible to increase the life of a pair of dies to an average of 1.5 million coins produced. In fact, an incredible 14 million coins were produced with a single record die.”
Therefore, as few as 289 pairs of dies were needed to produce all 420 million Croatian euro coins on time. This achievement earned the Croatian Mint, together with INORCOAT, a place among the finalists of the prestigious IACA Award 2023.
Dies from the Bavarian State Mint with Eco-Friendly Coating
Since 2024, Munich’s oldest company – the Bavarian State Mint – has also been using this new technology. It was not only the new law that prompted the move, but also a sense of responsibility towards its employees. Günther Waadt describes the extent of the risk to their health as follows: The risk is demonstrated by the fact that “the employees responsible for chromium electroplating have to undergo an annual medical check-up that must be continued even after they left the workplace.”
Although the Bavarian State Mint is an institution of national importance and would certainly have obtained an authorisation, Günther Waadt decided not to go through this time-consuming process and instead purchased a PVD system from INORCOAT. This makes Munich the third state mint to use such a system, after Portugal and Croatia, and closely followed by the Mint of Poland and other private mints. This is also due to the fact that it is becoming increasingly important for state companies to commit to sustainability goals in their production process. Günther Waadt explains: “We have been ISO 14001 certified since 2006, with all that this entails. We record consumption, set environmental targets, we know how many KWh it takes to produce a 1-cent coin, and keep records of CO2, nitrogen oxide (NOx) and particulate emissions. … This is why we decided not to continue with electroplating and to introduce a PVD system instead – even though the process is very complex compared to the well-established electroplating, and there is still little empirical data available.”
This data was collected together with Romain Waidelich of INORCOAT.
Romain Waidelich: Passion for PVD
In Romain Waidelich, the Bavarian State Mint found a partner who is passionate about PVD technology. Passion for PVD – that is the motto of the qualified industrial clerk who turned his company INORCOAT into a technology leader. He owes his extensive knowledge not only to his studies at renowned universities in Germany and France, but also to more than 20 years as a technical professional in the world of industrial engineering and, of course, the PVD industry.
Romain Waidelich decided in December 2018 to found his own company, the owner-managed INORCOAT. Since then, the firm has made rapid progress. The European company with locations in Germany and Bulgaria will add a new production hall in Przeworsk, Poland, in the third quarter of 2025. The building permit for the 700 square meter hall has already been issued, and construction will start in February 2025.
5-7 months to start operations in a completely new production facility – this sumps up Romain Waidelich perfectly. He is always on the move, full of new ideas and constantly looking for new challenges. He enjoys working with customers, helping them to convert their production processes to PVD coating. Despite Günther Waadt’s reservations, this also worked perfectly in Munich, as Romain Waidelich recounts: “The collaboration with the Bavarian State Mint was excellent. Thanks to the good preparation, the coating system was up and running within two days, and after a week the normal production process could begin.”
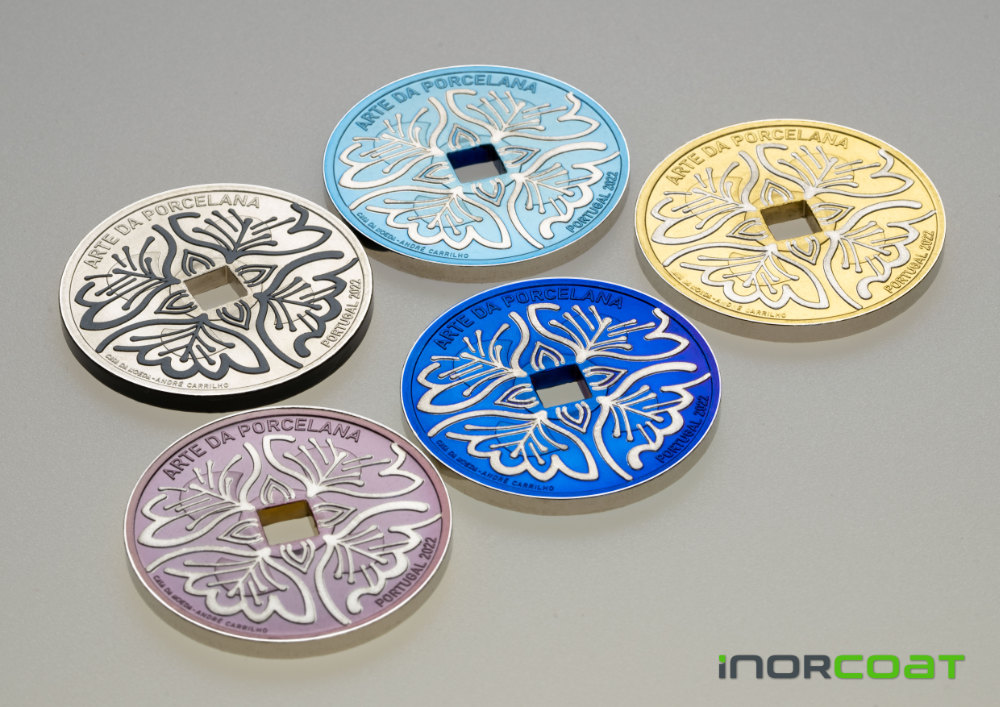
PVD coating can be applied not only to coin dies but also to coins themselves. This provides additional protection and also allows mints to use a wide range of colours, as these coins from the Portuguese mint impressively demonstrate. Photo: INORCOAT.
A Technology of the Future
It will be exciting to see what comes next. Because, as Romain Waidelich says: “This is just the beginning. In the coin industry, PVD is now a technology that nobody can ignore. And I already have lots of other ideas about what our systems could be used for.”
We could not agree more. Musicians, for example, are already using instruments with PVD-coated components. The long-established Bavarian company Schaller, which has been producing electric guitars and components for artists such as Jimi Hendrix and Keith Richards since 1945 did not want to go through the bureaucratic process of obtaining a permit for chromium electroplating. In 2024, two INORCOAT systems were installed there.