Bulmint
by Ursula Kampmann, translated by Maike Meßmann
Founded in 2004, Bulmint Group is now one of the up-and-coming market players in the field of bullion objects. Their production facilities are located in Plovdiv, Bulgaria. Under one roof, they combine everything that is necessary for the production of coins and ingots made of gold and silver: from refining the precious metal to minting and packaging the final product.
Content
In March 2023, I visited Plovdiv and Bulmint. It was a great experience to walk through all the departments within a few hours to see how a perfect bullion coin is created from the precious metal-bearing ore of the mine. I was particularly impressed by the company’s determination that is currently transforming Bulmint into one of Europe’s most modern private mints. Bulmint’s Technical Director Thomas Köninger comments: “Since I started here, not a month has gone by without me putting a new machine or production system into operation. We are constantly working on increasing our capacities while continuing to meet the high-quality standards of our customers. And this is indeed necessary because our products are in high demand. We are currently supplying blanks and bullion coins to seven countries on four continents. They are all produced entirely in-house – from refining the base metal to packaging the final product according to the customer’s preferences.” Ana Divarova, Chief Marketing Officer, adds: “Of course, we also distribute our own bullion products and collectibles through our shops and our website. Therefore, we know exactly what the customer wants.”
A Bulmint Tour
Ana Divarova and Thomas Köninger accompanied me on my tour. We did not start in the main building itself but in the place where Bulmint came to life in 2004 when engineer Plamen Zapryanov and scientist Dr. Ivan Panov founded a high-tech metallurgic company that specialized in the production of precious metal products. After Vladmir Spasov joined the management in 2011, the company repositioned itself focusing on numismatic investment products and ingots. Nowadays, the former production hall of the first Bulmint houses the state-of-the-art refinery.
Refining
To avoid any kind of misunderstanding: refining refers to all the steps that are necessary to purify ore, scrap metal or other base materials in order to be left with gold or silver – the raw material that is later turned into Bulmint’s products. For this purpose, Bulmint purchased brand-new machinery last year, which can extract several 100 kilograms of silver and gold of the highest purity per week. At present, the plant’s capacities regarding gold extraction have not been fully tapped yet; with regard to silver, Bulmint has already reached its limit once again.
Casting
The next step is casting. As this is carried out in-house, Bulmint can provide their customers with whatever alloy they prefer. Be it the highest purity of 9999.9, sterling silver, .900 silver or .333 silver, which is often used for the blanks of commemorative coins – the needs of all customers are catered for.
At present, a continuous casting process is employed to create thick plates that are then rolled into metal sheets, from which the blanks are punched out. There are advantages to this process, but also disadvantages. After all, especially when producing large amounts of blanks, working with coils – metal sheets that are coiled after the rolling process – would be more efficient.
Therefore, a machine to produce coils has already been ordered. It will be delivered in summer. So Bulmint will soon be able to offer two alternative options: to fulfil specific requests of their customers, the production of metal sheets will be continued; coils will be the more suitable option for mass orders.
Bulmint is particularly proud of one fact: extra-large blanks for bullion coins of more than one kilogram are not sintered or pressed at Bulmint, they are manually cast piece by piece. The cast ingot is then turned into the blank on a lathe. As Thomas Köninger explains, even experts are amazed by the results: a lack of cavitation and excellent surface qualities.
Rolling and Annealing
But let us get back to the plates that are currently being produced. They will be rolled and annealed. This is how the metal sheet is created, from which blanks are to be punched out later. This requires the metal to be rolled 8-10 times: with each step, the slab’s thickness is decreased by about 1.2 to 2 mm. This densifies the metal to such an extent that it would break in the following minting process. Therefore, its hardness must be reduced after rolling at 600-800 degrees Celsius under inert gas.
The annealing process causes the metal to recrystallize, with the result of a new structure of the material. This is of utmost importance as this is the only way to ensure that both a high relief and the delicate details of the coin design can be transferred onto the metal in the best way possible.
Inert gas incidentally refers to a mixture of gases that keeps the oxygen and the particulate matter contained in the air away from the metal. This ensures the purity of the surface and improves the blank’s quality.
Bulmint takes special pride in the fact that even the thin oxide layer that results from this process is removed by careful brushing. In this way, an even higher quality is achieved.
The next step is skin-pass rolling (also called temper rolling). Over 2-3 rolling cycles, the final thickness of the metal sheet is achieved. The maximum deviation is 0.005 mm. This corresponds to about one tenth of the diameter of a hair. This degree of precision is crucial because – in addition to the diameter and the predefined alloy – the thickness of a blank is the most important aspect that determines its fineness. And, of course, only blanks of perfect weight or with positive deviation will be delivered to customers. Bulmint obviously does not want to burden any end customer with a bullion coin that is too light.
After that, all metal sheets are straightened again because they do deform a little during the rolling process. Then they go to the next department.
Blanking
As the name suggests, blanking refers to the actual production of blanks. It is basically like cutting out Christmas cookies, just automated and with a little more noise. Thomas Köninger explains that this department will also be in a position to efficiently produce large batches of blanks within half a year: “We already have the system needed for this. We just have to put it into operation as soon as the continuous caster and the rolling mill can produce coils. I look forward to it because the amount of scrap metal will be significantly reduced. We currently use 52-54% of the metal to punch out the blanks, with an optimized coil, that figure will go up to 78-80%. So far, this did not play a big role for us because we immediately melt down the scrap metal again, which does not require much effort. But in the end, and especially regarding large batches, a coil will be more efficient.”
Thomas Köninger is very proud of the fact that Bulmint is in a position to always provide customers with a solution that is tailored to them. He says: “Although it is efficient, a coil is not suitable for everything. Special cases may require a different approach, for example because the requirements regarding surface quality and finishing are completely different for small series. We offer both: a motorway for large, extensive orders; and a country road for small, special requests.”
Quality Assurance
After the blanking process, an initial quality check is carried out – so far by hand and with the human eye. But this will change soon. Bulmint plans to switch to fully automated weight and defect control in the 4th quarter of 2023.
Edge Rimming
The next step is edge rimming, and there is a good reason why it happens at this point. Namely, a rim is necessary for effective degreasing and polishing as this takes place in large liquid tanks. Without a rim, the individual pieces would stick to each other or to the container due to the moisture adhering to them.
Be it a simple upset rim, complex edge lettering or other security features: with three RS50 systems by Schuler, Bulmint offers everything that is currently possible in this field.
Surface Treatment
The next step is crucial to prepare the blanks for the minting process. In a Spaleck system, water, centrifugal force, variously shaped media (abrasives) and chemicals are used to degrease and polish the blanks. Depending on the quality and quantity demanded, Bulmint offers several options. With the Z11 and the Z25, six people can clean up to 120-150 kilos of blanks per hour. For large batches, the Z44 is the way to go. In this scenario, a single person can process up to 2 tons of blanks per hour. Of course, there is not only a difference in speed but also in the efficiency.
Within this year, it will be possible to directly forward cleaned blanks from the Z44 to the station for surface quality control, and have them then be stacked for automatic minting.
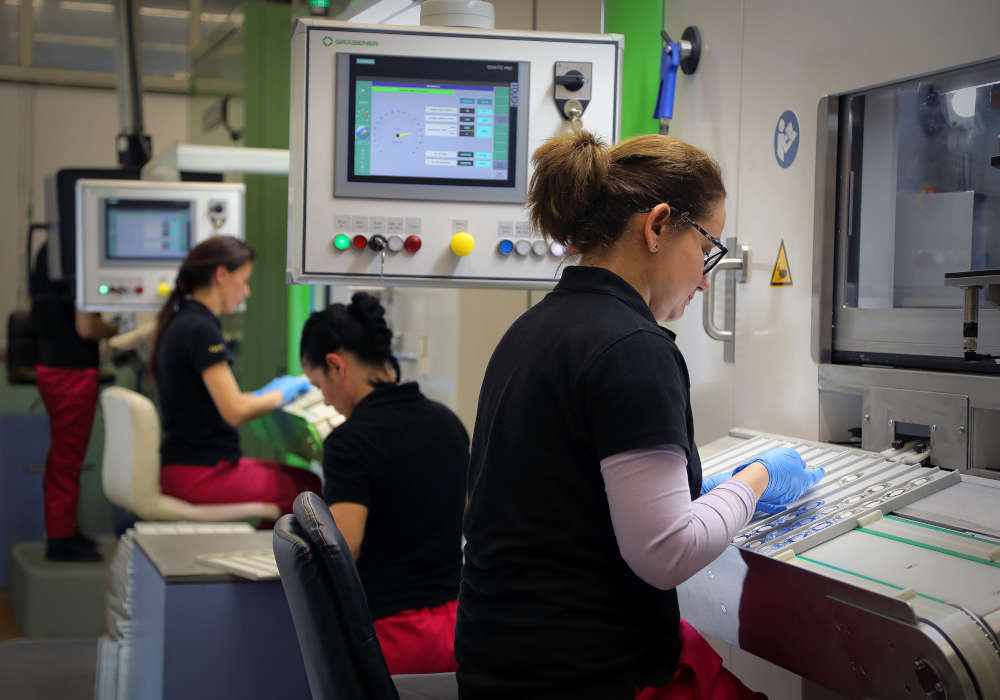
Bulmint has state-of-the-art minting presses of Gräbener and Sack & Kiesselbach for the production of high-quality bullion and collector coins. Photo: Bulmint.
Minting
Now we have finally arrived at the minting process. Bulmint currently works with three Gräbener minting presses. They produce about 100,000 bullion coins per day.
In addition, a brand-new oil-hydraulic press by Sack & Kiesselbach was being delivered during my visit. With a force of 1,250 tons, this press is mainly used for heavy blanks in the kilo range.
For smaller series of high-quality collector coins, two additional TMAs by Sack & Kiesselbach will be delivered in mid-2023. Thanks to the simple and quick handling of the machine, it is perfectly suitable for small coin series.
In-House Toolmaking
By the way, all tools are also produced in-house at Bulmint. They have their own designer who turns the ideas of customers and the marketing department into sophisticated designs, which are then transferred onto the die. Two milling machines fulfil this task – a mechanical mill and a laser mill. Bulmint prefers to mix both methods to combine the high relief of the mechanical mill with the laser’s precision to create an impressive die.
“Actually”, Thomas Köninger explains, “we only buy the steel. The rest in produced in-house. The system to create the environmentally-friendly PVD coating of the die is also ready to be put into operation. Then we will also have full control of die production.”
Colour Printing
The fact that Bulmint naturally also has a UV printing machine to colour collector coins will only be mentioned as a side note at this point.
Packaging
We have arrived at the last stop for all bullion coins and ingots before they are sent to the customer: final control and packaging. This is currently done manually because every customer wants to have their products packaged according to their special requests.
The company has its own haulage company for international shipping. When something has to be shipped within the country, they have an in-house security firm that drives up in the Bulmint security van for large orders.
Thomas Köninger concludes: “I have been fascinated by the fact that I deal with all aspects of bullion coin and ingot production here. That is highly demanding from the technical point of view as well as extremely multifaceted work. Transforming a mint such as Bulmint into a technical hub for the bullion and ingot sector really is a dream job. Due to our organization, we have complete control within our closed system in terms of quality and processes – and that obviously also has an impact on the costs for end customers. Anyone interested in bullion coins and ingots should have Bulmint on their radar.”
I could not agree more. Rarely have I seen such a dynamic company, where I could virtually watch processes being optimized. And it was the first time for me to witness ALL steps of coin production under a single roof. There are many images that will come to mind the next time I see the Bulmint logo.
Latent images, micro inscriptions, holograms: This article is about modern minting technologies.